【如何管好供应商】
1供应商选择的影响因素
供应商隶属于供应链这一个开放的系统,因而供应商的选择也会受到各种经济、政治和其他因素的影响 。
1.1质量因素
质量是供应链的生存之本 , 产品的使用价值是以产品质量为基础的,它决定了最终消费品的质量,影响着产品的市场竞争力和占有率 。因此,质量是选择供应商的一个重要因素 。
1.2价格因素
价格低 , 意味着企业可以降低其生产经营的成本,对企业提高竞争力和增加利润,有着明显的作用,是选择供应商的重要因素 。但是价格最低的供应商不一定就是最合适的,还需要考虑产品质量、交货时间以及运输费用等诸多因素 。
1.3交货准时性因素
能否按约定时间和地点将产品准时运至直接影响企业生产和供应活动的连续性 。也会影响各级供应链的库存水平,继而影响企业对市场的反应速度 , 打断生产商的生产计划和销售商的销售计划 。
1.4品种柔性因素
要想在激烈的竞争中生存和发展,企业生产的产品必须多样化,以适应消费者的需求,达到占有市场和获取利润的目的 。而产品的多样化是以供应商的品种柔性为基础的,它决定了消费品的种类 。
1.5其他影响因素
包括设计能力、特殊工艺能力、整体服务水平、项目管理能力等因素 。
2供应商的选择方法
目前 , 可以应用于供应商选择的技术方法和工具主要分为三类:定性方法、定量方法及定性与定量相结合的方法,具体有公开招标法、协商选择法、ABC 成本法、线性规划方法、层次分析法(AHP)、模糊综合评判法、神经网络法、TOPSIS 法、数据包络分析(DEA)、成分分析法、灰色综合评价法以及这些方法的集成应用法等,制造型企业可以根据自己的实际情况选择其中的方法加以应用 。常用的方法如下:
1 直观判断法
直观判断法是指通过调查、征询意见、综合分析和判断来选择供应商的一种方法,是一种主观性较强的判断方法 , 主要是倾听和采纳有经验的采购人员的意见 , 或者直接由采购人员凭经验作出判断 。这种方法的质量取决于对供应商资料掌握得是否正确、齐全和决策者的分析判断能力与经验 。这种方法运作简单、快速,但是缺乏科学性,受掌握信息的详尽程度限制 , 常用于选择企业非主要原材料的供应商 。
2 考核选择法
在对供应商充分调查了解的基础上 , 再进行认真考核、分析比较而选择供应商的方法 。
供应商的调查可以分为初步供应商调查和深入供应商调查 。每个阶段的调查对象都有一个供应商选择的问题,而且选择的目的和依据是不同的 。
初步供应商调查对象的选择非常简单,基本依据就是其产品的品种规格、质量价格水平、生产能力、运输条件等 。在这些条件合适的供应商中所选择出的几个,就是初步供应商调查的对象 。
深入供应商调查对象的选择,是基于影响企业的关键产品、重要产品的供应商 。对这些供应商要进行深入地研究考察考核,选择标准主要是企业的实力、产品的生产能力、技术水平、质量保障体系和管理水平等 。
在对各个评价指标进行考核评估之后,还要进行综合评估 。综合评估就是把以上各个指标进行加权平均计算得到的一个综合成绩,可以用下式计算:
S=∑WiPi/∑Wi×100%
其中:S是综合指标;Pi是第i个指标;Wi是第i个指标的权数,根据各个指标的相对重要性而主观设定 。S作为供应商表现的综合描述 , 值越高的供应商表现就越好 。
通过试运行阶段,得出各个供应商的综合成绩后 , 基本上就可以最后地确定供应商了 。
3 招标选择法
当采购物资数量大、供应市场竞争激烈时,可以采用招标方法来选择供应商 。采购方作为招标方,事先提出采购的条件和要求,邀请众多供应商企业参加投标,然后由采购方按照规定的程序和标准一次性的从中择优选择交易对象 , 并提出最有利条件的投标方签订协议等过程 。注意整个过程要求公开、公正和择优 。
4 协商选择
在可选择的供应商较多、采购单位难以抉择时 , 也可以采用协商选择方法,即由采购单位选出供应条件较为有利的几个供应商,同他们分别进行协商,再确定合适的供应商 。和招标选择方法相比,协商选择方法因双方能充分协商,因而在商品质量、交货日期和售后服务等方面较有保证,但由于选择范围有限 , 不一定能得到最便宜、供应条件最有利的供应商 。当采购时间较为紧迫,投标单位少,供应商竞争不激烈 , 订购物资规格和技术条件比较复杂时,协商选择方法比招标选择方法更为合适 。
供应链管理随着时代的变化 , 向企业提出了动态管理、科学管理、数字化管理的挑战,要求企业必须建立一套行之有效的科学管理办法,管理企业内部和供应链,方能在日渐激烈的市场竞争中持续存活与发展 。
今天和大家分享一下海岸线基于DQRTC模型,提出的供应链中供应商的评级评分体系与DQE、PQE/MQE、SQE相关的指标 。
下文主要描述Q、T指标:
Q(Quality)质量指标
作为SQE最重要的数据支撑指标,它包括:
供应商来料批次合格率(合格来料批次/来料总批次×100%)、来料抽检合格率(来料抽检合格总数/抽检样品总数×100%)、来料全检合格率(来料抽检合格总数/抽检样品总数×100%)、来料在线报废率(来料生产时报废数量/来料总数×100%)等 。
随着行业的发展和数据的协同 , 质量指标也日益丰富 。
如供应商的出货检验(OQA)、产线制程能力检验(IPQC)、制程终检(FQC),甚至供应商的来料检验(IQC)都已纳入质量指标中 。
此外,由于技术的发展和企业对质量的愈发重视,单件质量在越来越多的场景中成为可能,它将代替平均质量成为质量数据的风向标 。
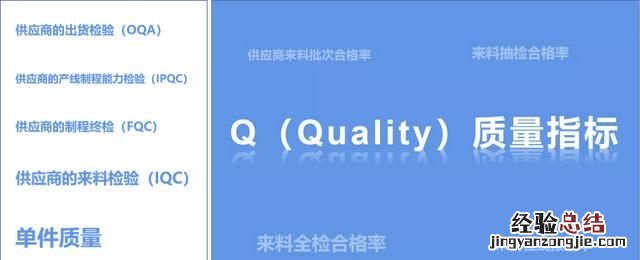
不久的未来 , 在供应链质量数据大协同的背景下,免检会成为趋势,最优社会资源配置的高质量JIT库存将越来越成为可能与可信 。
T(Technical)能力指标
任何一款成功产品的面世都是整个供应链的成功,因此产品的研发,不仅仅是公司内部的研发,更是供应链的协同研发 。
供应链的制程能力指标,需要科学管理办法和科学管理工具双管齐下 , 根据不同品类定义关键制程指标,合理获取数据、分析数据,既要尊重供应链企业的机密信息,又能作为供应链企业的评级评分维度 。
质量是结果指标,却关联着过程,反馈着过程管理办法的失效与否,有诊断有改善 , 用结果反哺过程,用过程,重新定义结果 。