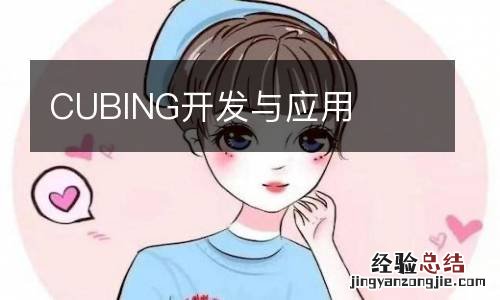
该文通过对车身主检具CUBING的介绍与分析,着重阐明了在CUBING设计时所遵循的各项原则,加工制造时所需要保证的加工精度要求,以及在装配检测过程中的各项问题 。
1 CUBING结构概述
1.1 概述
车身主检具CUBING是一个高度模块化检具,可根据需要自由设计或匹配检查项 , 所有模块和零部件均可自由拆换 。目前较常见的分类为整车式和分体式结构;其中整车式结构可以实现钣金件,内、外饰件等的安装匹配检测;而分体式采用局部钣金件 , 内、外饰件匹配检测 。可大幅度降低加工制作成本(常运用在年度车型开发阶段) 。
1.2 结构分类:
1.2.1 整车式(UCF)
整车式(UCF)包括:车身主量具部分(BMG)和零件主量具部分(PMG) 。车身主量具(BMG)一般包括:车体、引擎盖焊接总成BMG、翼子板、前门焊接总成、后门焊接总成、尾门焊接总成等;零件主量具部分(PMG)一般包括:外饰部分(PMG)和内饰部分?D车体安装部分(PMG) 。其中 , 外饰部分包括前组合灯具总成、前保险杠总成、后保险杠总成、后组合灯总成、尾饰灯总成、前挡风玻璃总成、后窗玻璃总成、前罩铰链总成、前后车门铰链、尾门铰链总成、尾门饰板本体总成和油箱盖锁舌 。内饰部分?D?D 车体安装部分(PMG)一般包括转向支撑,A立柱内饰板 , 前门槛装饰件,B立柱上内饰板,C立柱上内饰板,前门内饰板总成,尾门左右内饰盖板,后门槛装饰件总成和背门槛装饰件总成 。
1.2.2 分体式
分体式(也可称UCF)结构包含整体式内单项的部分组合 , 例如:前脸UCF,后脸UCF 。
2 CUBING设计考虑因素
2.1 设计资料
CUBING设计主要依据是产品3D数模、DTS图纸、GD&T信息及整车测点图 。整车式UCF上所有BMG、PMG间的间隙值、高差值按照DTS图纸设计;DTS图纸上未体现的配合面按照带GD&T信息的产品3D数模设计 。所有需安装到实车上的BMG、PMG的定位基准、安装基准按照2D图图纸信息进行设计,以保证基准的统一性 。产品零件在车体BMG上安装时的定位孔、定位面等应与车身实际状况一致 。
2.2 结构设计考虑因素
?。?)结构上合理可靠、操作方便,能够满足功能要求 。
?。?)功能主检具应有足够的强度和刚性,并尽可能采用轻量化设计、制造 。
?。?)加工负角的处理和过渡,需要满足装配和检测需求 。
?。?)多曲面加工,设计时需考虑其加工定位选择 , 要满足装配和检测需求 。
?。?)功能主检具及各标准模块采用材质为铸铝、航空铝,考虑其加工定位选择 。
?。?)能保证标准模型件及实物零部件取放、装夹、搬运等操作方便 。
?。?)功能主检具应配有起吊装置或滚轮,方便叉车运输 。还应有起吊装置、夹紧器、专用量规以及其它配件等 。
?。?)零部件的形状面,其夹紧力大小以被测零部件能保证贴合在检具的定位面上为准 。
?。?)零部件定位面的工作面其位置应分布合理,保证定位可靠,并且便于测量 。
?。?0)每个独立的(标准)模块均应有车身坐标系下可用于测量的检测基准 。
?。?1)每个模块的坐标值标牌均采用车身坐标值 。
2.3 材质
CUBING加工行业内多采用:UCF\BMG:铸铝牌号7000系列,采用铝合金消失模树脂砂型铸造;PMG\BMG:6061航空铝;基板及框架:Q235 。
2.4 规格要求
功能主检具CUBING在线检测时要操作方便,装卸结构要稳定可靠,操作高度与人体高度、测量机行程适宜 。检具标示其车身坐标理论位置,便于三坐标测量作为基准进行矫正补偿 。每一部分独立的功能匹配检具的整体要配置移动轮和吊装装置,以及叉车孔的位置 。功能主检具的外观匹配表面画有整百坐标线 , 并在相应部位标示出标准的面差值和间隙值 。每一部分独立的功能主检具的整体要有标牌 。每一个模块间的理论缝隙值、模块的安装位置、模块的截断位置、模块上的附属件及模块的编号等内容要附有明确标牌指示说明 。
3 CUBING主要模块加工
3.1 加工方式
车身主检具对型面尺寸位置精度有着较高要求,其主要采用CNC加工 , 对于要求很高的部分(例如:前大灯)甚至需要用5轴机床加工 。其中为保证加工精度,工序分为粗加工、半精加工、和精加工3道工序,后4~5次翻面 。在粗加工完后尽心消除应力处理其中包括人工时效处理和振动时效处理,在切削量上以少量多次为原则保证,减少加工过程中的应力和变形 。
3.2 加工精度要求
车身主检具不仅要求有单件的要求,而且在总装配时 , 对整体装配精度也十分严格;目前对于要求比较高的厂家,对A面的检测也必须体现在主检具上 。目前大部分精度要求如下:基准面的平面度≤0.05 mm/m;基准孔的位置精度≤±0.08 mm;定位活动件配合精度H7/g6或H7/f6;产品件的安装孔位置精度≤±0.2 mm;模块的安装孔位置精度≤±0.1 mm;模块的匹配缝隙精度≤±0.1 mm;模块的功能区表面精度≤±0.2 mm;模块的非功能区表面精度≤±0.2 mm(要求光顺);重复安装精度≤±0.1 mm;一般安装匹配部位的位置精度≤±0.2 mm 。
4 CUBING装配与检测
4.1 单件检测
单件检测是尺寸精度控制的关键,只有保证单件合格,才能够保证总装配的精度 。
地板、骨架的检测:可以完成基准孔、定位孔、基准面、安装面等形位误差和尺寸偏差 。
4.2 总装检测
总装检测主要是功能面、型面以及匹配的间隙(GAP)、面差(FACE)检测 。总装检测同时根据精度检测值进行适当的调节,合理分配公差以保证整体精度与间隙、面差精度的协调与合理 。而BMG及PMG中 , 车灯轮廓周边不少于30 mm的精加工范围 , 以保证高精度对应匹配检测,其它PMG、BMG的轮廓周边不少于40 mm的精加工范围 。
4.3 实物的匹配
将模块逐次更换成实物,检查实物的装配、定位,确认干涉 , 以及实物与模块制件的匹配,确认功能面的问题 。
5 结语
车身主检具是对车身三维数模与量产车型之间一致性的精确评价,是在量产工装之前实行的一次真正意义上产品的实物验证 。也对车身开发及量产过程中车身匹配问题点的校验 。另外,主模型造不出来或者较难造出来或者较容易造出来,本身就从某种意义上代表着项目的成功程度 。故主检具的使用使主机厂在项目可行性分析时受益匪浅 。合理选择所需部分组合开发 , 对于解决实际问题点提供了经济而行之有效的途径 。该文在CUBING的宏观设计和使用方面进行简单的阐述,对于内部详细的功能、结构还未深剖 。该领域还有大量知识待我们去进一步学习研究 。抛砖引玉,希望更多专业人士提出深刻见解,为振兴民族汽车工业提供源源不断的力量 。【CUBING开发与应用】